Continuous Gum Conditioning Section :
Centrifugal Separator:
SHFT make hermetic centrifugal separator, with body in cast iron & all oil contact parts in stainless steel. The solid bowl separator has better separation efficiency. With less maintenance. The separator is provided with manual interface selection fort he exact phase separation of heavy and light liquid. Hence less loss of valuable oil and much improved operational economy
The crude oil from bulk storage tank, is directly pumped to the set of alternating operating neutralizers. Initially it will act as homogination cum buffering tank, further oil is getting heated up to required temperature for gum conditioning operation, then pre-calculated amount of phosphoric acid is getting added manually.
Further this is hold for certain time & then pumped to the Centrifugal separator for removing gums Neutralizer is fully equipped with steam heating coils, acid spraying coil and mechanical agitation, complete with electrical motor & gear box.
Continuous Bleacher Section :
De-gummed oil form is pumped to the OIL EARTH MIXER Pre-calculated amount of bleaching earth is added in the OIL EARTH MIXER.Further this oil will be sucked by means of vacuum to the Continuous BLEACHER (E-502). ‘PHOENIX’ Bleacher is a multi-compartment vessel, which is having drying, heating, agitation& sparging arrangement.After proper holding & mixing this oil is sent to the alternative operating set of PRESSURE LEAF FILTER ( PLF 1 & PLF 2 ) after this filtration oil is again filter by alternative operating set of polishing filters. then it is cooled by shell and tube cooler before it reaches to the BOT.
Benefits of ‘PHOENIX’ Bleaching Section:
Continuous De-Waxing Section :
PHOENIX’ offers a wide range of batch & continuous De-Waxing Plants. Most of the natural oils & fats have only a limited applications in there original forms as a consequence of there specific chemical composition. In order to widen there uses the oils goes through variety of modifications, Fractionation is one of them.Fractionation is the fully reversible modification process. It is basically a thermo-chemical separation process in which a multi-components mixture is physically separated in to two or more fractions with distinct physical & chemical properties. The can be based on a difference in solidification, solubility, or volatility of different compounds.
PHOENIX”s De-Waxing plant is a custom design to allow you to achieve selective crystallization of different triglycerides in edible oil. This is plant you can count on producing stable & filterable crystals giving you a product to fit your standards and quality requirements.
PHOENIX’s system is designed to process Bleached Rice Bran oil. The process is divided in few steps as below:
Continuous Physical Deodorizing Section:
Deodorizing is nothing but The DISTILLATION process. in which fatty acid is distilled from oil. Under high temperature condition and in presence of high vacuum, with the help of sparging & agitation steam. Further this fatty acid in vapors form, is condensed &recovered in liquid form by the vapors scrubbing system. Bleached oil from intermediate storage tank is pumped by) to oil to oil heat exchanger Where bleached oil is getting heated by the outgoing hot refined oil. Then this oil is going to The PRE-HEATOR Via. Peripheral coils of the regenerative heat exchanger which is the bottom compartment of the multipurpose deodorizer.In regenerative heat exchanger de-waxed oil flows through the coils & refined oil flows through the open space of the exchanger. In counter current manner, continuous steam agitation at open steam side assures continuous and maximum heat exchange.
After recovering maximum heat from the refined oil. Oil is further heated up to the required temperature, suitable for the deodorizing in final heater. This heater is equipped with agitation and sparging steam, continuous flow of superheated steam through this assures effective primary vaporization of fatty acid. Further this overflows to the multi-compartment DEODORIZER Deodorizer is multi-compartment vertical vessel, where each and every trays are specially designed which Ensures uniform distillation of odoriferous substances. Oil is overflows from tray to tray. Specially designed trays provide sufficient mass transfer surface for effective removal of volatile matters. Flow control system at the outlet of the deodorizer, ensures the maintenance of required level at the bottom tray. The steam used for stripping off volatile matters in the oil is distributed evenly and intensively.the steam meets the deodorized oil. Stripped off the volatile matter and rises through the vacuum. Stripping the volatile matter from the oil. The counter-current flow of steam and oil like this in specially designed trays lower steam consumption, than the conventional deodorizers. The deodorized oil leaving regenerative heat exchanger and finally cooled by water in heat exchanger finally this oil is passed through the alternatively operating set of polishing filters.
Vapors Scrubbing:
The volatile matters consisting of free fatty acid and other odoriferous substances stripped from the deodorizer are led to the vapor scrubber located at the outside of the deodorizing column. In the scrubber volatile material rises through the bed of pall rings and meets liquid fatty acid sprayed from the top.Vapors are condensed, cooled, and then recalculated to condensed fresh vapors. Excess distillate collected is led to the storage tank, whenever high level reached in storage space below the scrubber. Fatty acid scrubber is specially designed for minimum carryover of fatty materials, to the vacuum system.
Benefits of PHOENIX Deodorizing section :
- Great Technology
- Certified Engineers
- Delivery Ontime
- Best Branding
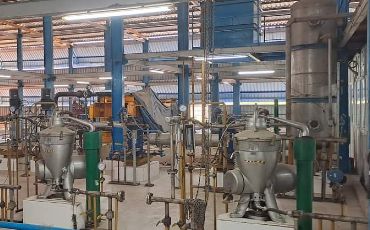
Salient Features of Vegetable oil refinery plant ( physical & chemical ):
here are some salient features of a vegetable oil refinery plant, both physical and chemical: